Pile Design and Management for Optimal Feedout
Perfect silage feedout management starts with your pile design. The shape and size of your pile help you to minimize losses at feedout by allowing optimal feedout rate, limiting oxygen penetration in the silage mass and keeping it cool and clean.
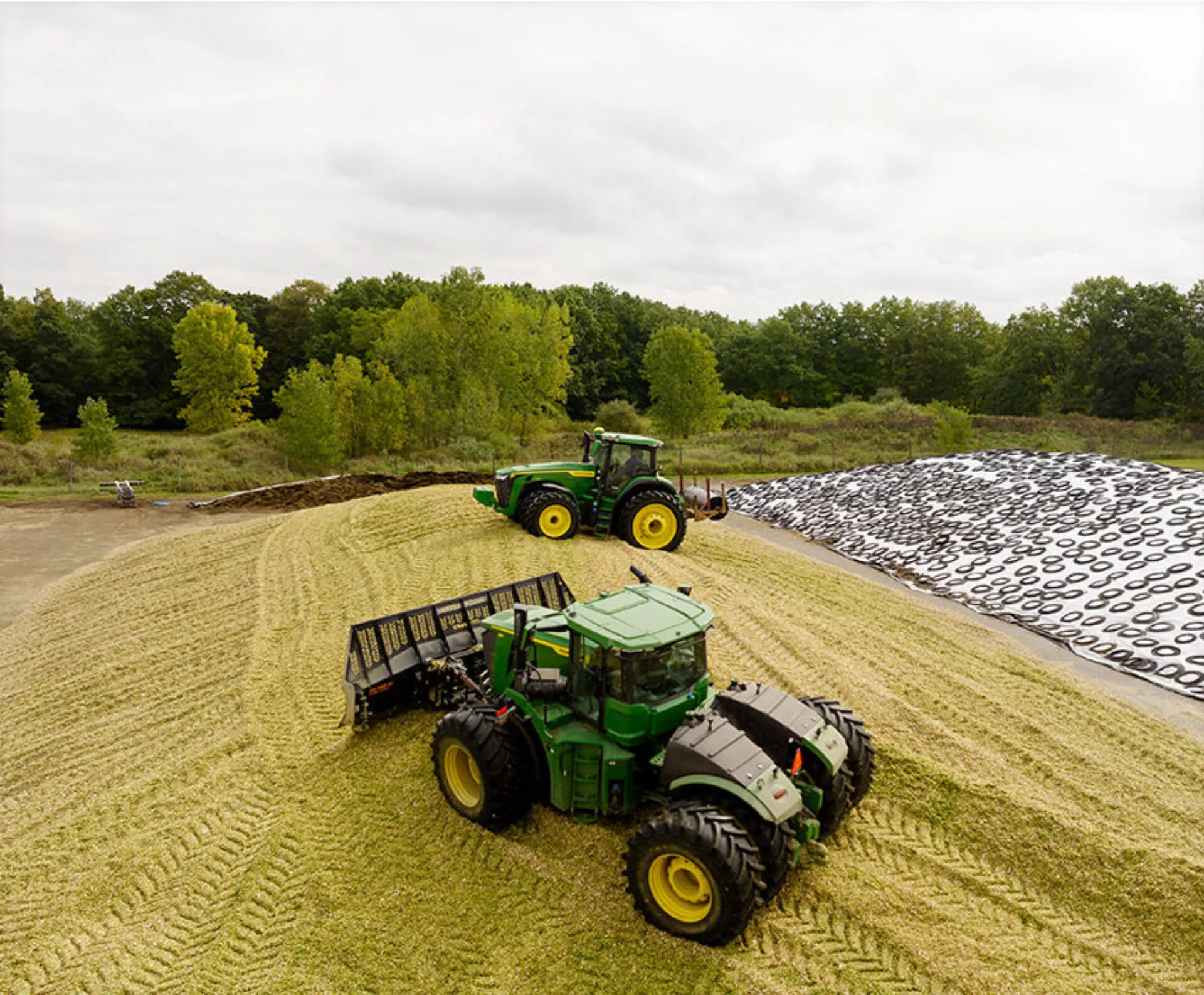
Once the silo is opened, the silage mass at the face is exposed and oxygen penetrates as much as three inches into the silo, and that’s where the danger begins. Yeasts are the primary spoilage microorganisms after air exposure of the silage. In the presence of oxygen, yeast utilizes lactic acid as substrate, increasing silage pH which is an opportunity for fungi growth. Designing a pile that allows greater feedout rates decreases the time that the face is exposed to atmospheric air, and, therefore, limits the growth of spoilage microorganisms.
FEEDOUT RATE MATTERS
It is important to design a pile that permits feedout of at least six inches of the face per day. However, piles with lower bulk density need greater feedout rates to avoid spoilage when compared to a higher density pile. For example, a pile with average density of 50 lbs/ft3 (as fed) needs four inches of feedout rate to have feedout losses at the maximum recommended loss (around 3%), while a pile averaging 30 lbs/ft3 (as fed) needs around seven inches of feedout per day to achieve the same 3% loss. Therefore, a feedout rate of minimum six inches per day is recommended to avoid spoilage across a variety of bulk density piles.
Figure 1. Graphical representation of theoretical reach of atmospheric oxygen through a well packed silage face. A feedout rate of at least six inches per day decreases the time silage is exposed to oxygen, therefore minimizing yeast activity.
Piles taller than the reach of your face-removal equipment will likely have a ledge remaining as silage is removed. This ledge is more prone to spoilage if exposed to air for longer and creates a hazard as it increases the likelihood of an avalanche accident.
Even though silage inoculation with L. buchneri helps keep silage cooler and free of spoilage for longer periods, it cannot overcome poor feedout management.