Back
Overcoming Challenges for Grass and Legume Silage
There are many potential reasons why grass silage may end up with an undesirable fermentation. Below is a list of common issues that arise during the process of making grass and legume silage and potential causes and solutions.
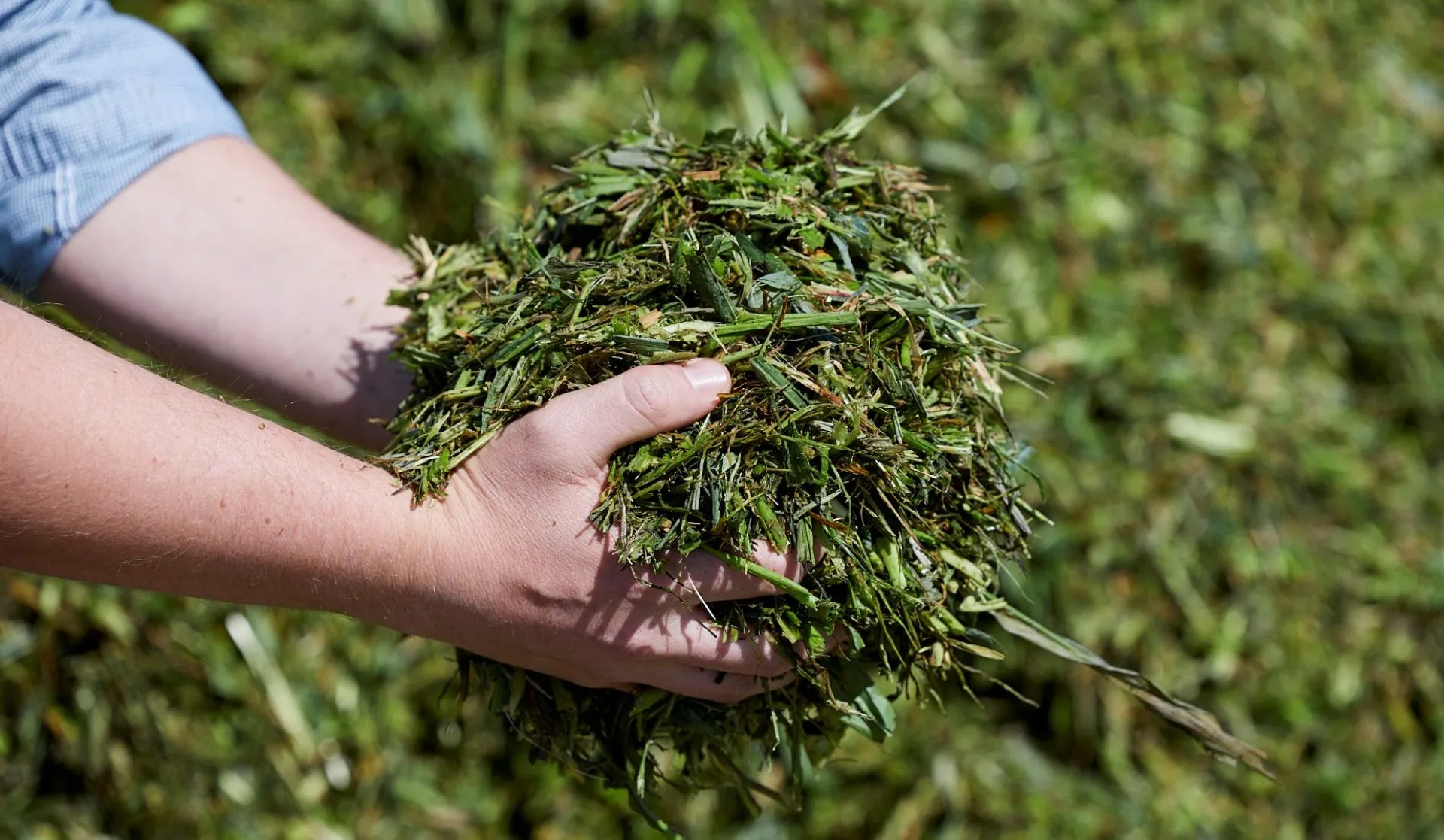
Reheating/mold immediately underneath the film
- Holes in the film e.g. caused by animals or weather
- Plastic with insufficient oxygen penetration protection
- No oxygen barrier
- No large tires or sandbags on plastic edges
- Silos should be wide enough to allow parallel unloading and packing of loads.
- Silos without side walls need to be designed wider, as the silage pile becomes narrower towards the top.
- Fill by layers.
- Each layer should not be thicker than 6 inches, as greater thicknesses makes it more difficult to pack the silage efficiently.
- Avoid unloading silage in piles in front or on top of a silo as it makes adequate packing particularly difficult. The extra time needed for spreading the large piles out can then be used for additional packing.
- Ensure that packing is performed as evenly as possible across the full surface. Having another tractor and driver available for pulling vehicles on top of the silage can be particularly useful.
Reheating/mold at the upper silo face
- Inadequate packing and compaction
- Improper packing (chop length, deposited layer sizes) and silo geometry do not match
- Improve packing and compaction, including chop length, pile planning, and depth of layers being packed
- Improve face management
Reheating/mold about 6-8 inches below the surface
- Excessively deep layers deposited at the top during packing
- Silage layer excessively contaminated with soil and dirt
- The top layer can be unaffected due to it being too cold for molds and yeast to grow
- Maximum 6 inch layers during packing
- Maximize compaction and increase packing density
- Avoid bringing in more ash (soil and manure) from the field
Reheating/mold in the middle of the silage
- Excessively high DM layer, or old excessively wilted material
- Unreasonably deep layers deposited at the top during packing
- Insufficient chop length
- Maximum 6 inch layers during packing
- Avoid introducing over-mature and/or excessively wilted material into the middle of your silage:
- instead ensile separately or deposit in thinner layers at the very bottom of the silo
Reheating/mold randomly distributed
- Insufficient chop length or distributed over-mature material (in combination with inadequate packing)
- Inconsistent silo filling and/or presence of cavities (trapped air)
- Harvesting residue from a previous cut – inadequate management
- Chop overly mature material shorter
- Fill silos evenly and avoid air pockets or “cavities”
- Avoid picking up material from previous cuttings
Reheating/mold around the edges
- Incorrect filling of silo bunks (sloped outside edges)
- Poor compaction along edges
- Pack right up to the silo wall
- Use sidewall and oxygen barrier plastic
Silage smells of butyric acid
- High contamination of ash (from soil and manure)
- Improper fertilization: a shortage of nitrate in plants as a natural inhibitor of clostridial growth during the ensiling process
- Improve harvesting hygiene, reduce soil and manure contamination
- Adjust fertilization
- Review silage additive use
Rotten, slimy layer on the surface
- Holes in plastic film, e.g. caused by animals or weather
- Long delay in covering silage
- Pockets of air between the plastic and silage
- Cover the silage as soon as packing is finished
- utilize an oxygen barrier
- Use a thicker main plastic
- Make use of silage netting or tarp to protect against mechanical damage